Mechanical seals are a vital component in rotating equipment, protecting systems from leaks and contamination. When a mechanical seal fails, the consequences can range from minor inconveniences to catastrophic system failures and significant downtime. Understanding the root causes of mechanical seal issues, their impacts, and the strategies to prevent them is essential for maintaining reliability and efficiency across industries.
In this guide, we’ll explore why mechanical seal failures occur, what consequences they can trigger, and how the latest mechanical seal technology and correct mechanical seal installation practices can significantly minimize these risks.
What is a Mechanical Seal?
A mechanical seal is a device designed to join systems or mechanisms together by preventing leakage, containing pressure, and excluding contamination. Used primarily in pumps, mixers, and compressors, mechanical seals play a crucial role in maintaining operational efficiency and equipment integrity.
Mechanical seals are preferred over traditional packing systems because they offer higher reliability, reduced maintenance, and longer service life. Advances in mechanical seal technology continue to push performance boundaries, offering better resistance to extreme pressures, temperatures, and corrosive environments.
Modern mechanical seals consist of several critical components, including seal faces, secondary sealing elements (such as O-rings), and gland plates, all of which must work in harmony under harsh operational conditions.
Types of Mechanical Seals
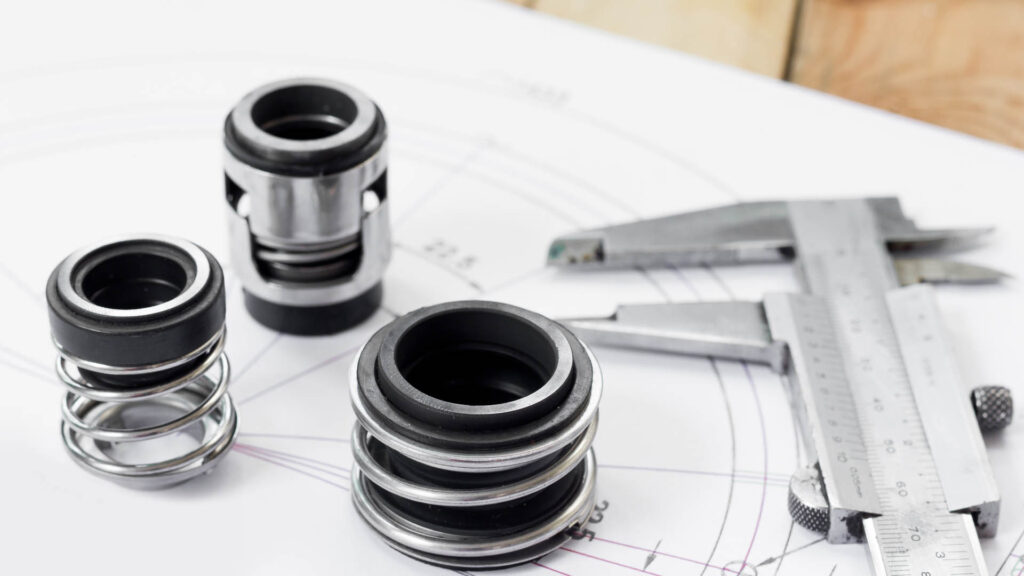
Choosing the right type of mechanical seal is critical to ensuring long-term equipment reliability. Different applications, operating conditions, and industry standards demand specific sealing technologies. Understanding the primary types of mechanical seals helps in selecting the right solution during mechanical seal installation and maintenance planning.
Here’s an overview of the main types of mechanical seals used today:
- Cartridge Seals
Cartridge seals are pre-assembled units consisting of the seal faces, gland plate, sleeve, and hardware. They are designed to eliminate common installation errors by simplifying the installation process of mechanical seals. Cartridge seals are ideal for operations that demand fast maintenance, reduced downtime, and higher reliability.
Advantages:
- Easy, error-free installation
- Factory pre-set compression
- Reduced maintenance time
Modern mechanical seal technology often favors cartridge seals for critical operations due to their consistency and ease of replacement.
- Component Seals
Component seals are made up of individual parts — seal faces, O-rings, springs, and gland plates — that must be assembled during mechanical seal installation. While they offer flexibility and customization, they require a higher skill level to install properly.
Advantages:
- Flexible design options
- Lower upfront cost
- Suitable for custom-engineered applications
However, improper mechanical seal installation of component seals can lead to alignment issues and premature failure if not handled by experienced technicians.
- Single Mechanical Seals
Single seals are the most common type and consist of one set of sealing faces. They are typically used in applications where leakage to the atmosphere is not critical or where fluids are non-hazardous.
Advantages:
- Simple design
- Cost-effective solution
- Widely available and versatile
Despite their simplicity, ensuring the right single mechanical seal technology is crucial for applications involving abrasive or volatile fluids.
- Double Mechanical Seals
Double mechanical seals consist of two sets of seal faces. They are used in more hazardous environments where leakage must be avoided at all costs. A barrier or buffer fluid between the two seals prevents process fluid from escaping.
Advantages:
- Enhanced leak protection
- Suitable for hazardous, toxic, or abrasive fluids
- Increases mechanical seal lifespan
Double seals are commonly used in the chemical processing, pharmaceutical, and food industries, where regulatory standards for leak prevention are strict.
- Bellows Seals
Bellows seals use flexible metal bellows to eliminate the need for dynamic elastomers, such as O-rings. They are ideal for high-temperature applications or chemically aggressive environments where standard elastomers would degrade.
Advantages:
- Excellent chemical and temperature resistance
- No dynamic O-ring that can stick or wear out
- Suitable for slurry or abrasive applications
Bellows seals are a significant advancement in mechanical seal technology, offering long-term reliability in some of the harshest operating conditions.
- Gas-Lubricated Seals
Gas seals, also known as non-contacting seals, use a thin gas film to separate the seal faces, reducing friction and minimizing wear. These seals are commonly found in compressors and other high-speed machinery.
Advantages:
- Virtually no face-wear
- Reduced energy consumption
- Extremely long service life under proper conditions
Gas seals represent some of the most advanced developments in mechanical seal technology and are essential in industries such as oil and gas, where performance and efficiency are paramount.
Common Causes of Mechanical Seal Failures
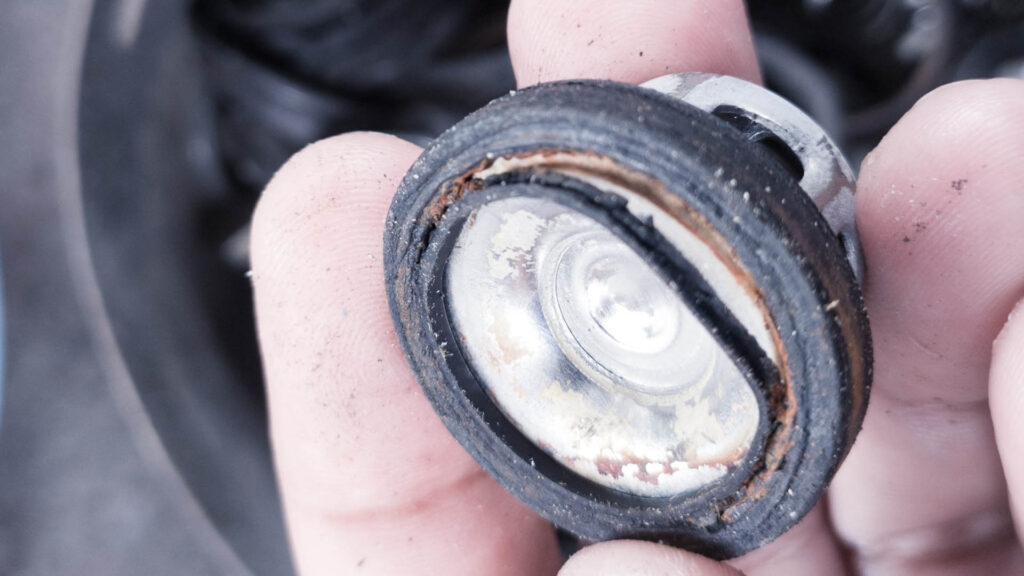
Even with the best mechanical seal technology, failures can still occur if specific conditions are not met. Here are the most common culprits:
- Improper Mechanical Seal Installation
Incorrect installation is one of the leading causes of premature mechanical seal failure. Misalignment, uneven torque, contaminated assembly areas, and incorrect handling can all introduce issues that lead to rapid degradation of the seal faces or elastomers. Improper mechanical seal installation can turn even the highest quality seals into liabilities.
It’s important to follow a detailed installation checklist and engage technicians trained in mechanical seal technology to mitigate these risks.
- Incorrect Seal Material Selection
Choosing the wrong materials for the application—whether it’s the seal face, secondary seals, or hardware—can result in accelerated wear, chemical attack, or thermal breakdown. Mechanical seals must be carefully matched to the operating environment to ensure longevity.
The chemical properties of the fluid, system pressure, and temperature range all influence material selection decisions.
- Dry Running
Mechanical seals require a lubricating film, typically provided by the pumped fluid. If a seal operates dry—even briefly, the frictional heat can crack or distort the seal faces, causing immediate failure. Mechanical seal technology advancements now integrate dry-run-resistant designs, but prevention is still key.
Seal support systems, like Plan 23 or Plan 52, can help ensure proper lubrication and cooling.
- Vibration and Shaft Deflection
Excessive vibration or shaft movement can disturb the delicate face-to-face contact of the seal components. This movement leads to accelerated wear and leakage, shortening the mechanical seal’s lifespan.
Frequent shaft alignment checks and vibration monitoring are essential parts of mechanical seal installation protocols.
- Thermal Shock
Sudden temperature changes can cause seal materials to expand or contract rapidly, leading to cracking, loss of sealing integrity, and, ultimately, mechanical seal failure.
Modern mechanical seal technology offers faces with different thermal expansion coefficients to better handle fluctuating conditions.
- Chemical Attack
Exposure to incompatible fluids can degrade seal faces, O-rings, and gaskets. Chemical attacks may not be immediate, but over time, they compromise the seal’s structure and performance.
Consulting with experts in mechanical seal technology during the selection phase prevents costly compatibility issues later on.
Consequences of Mechanical Seal Failures
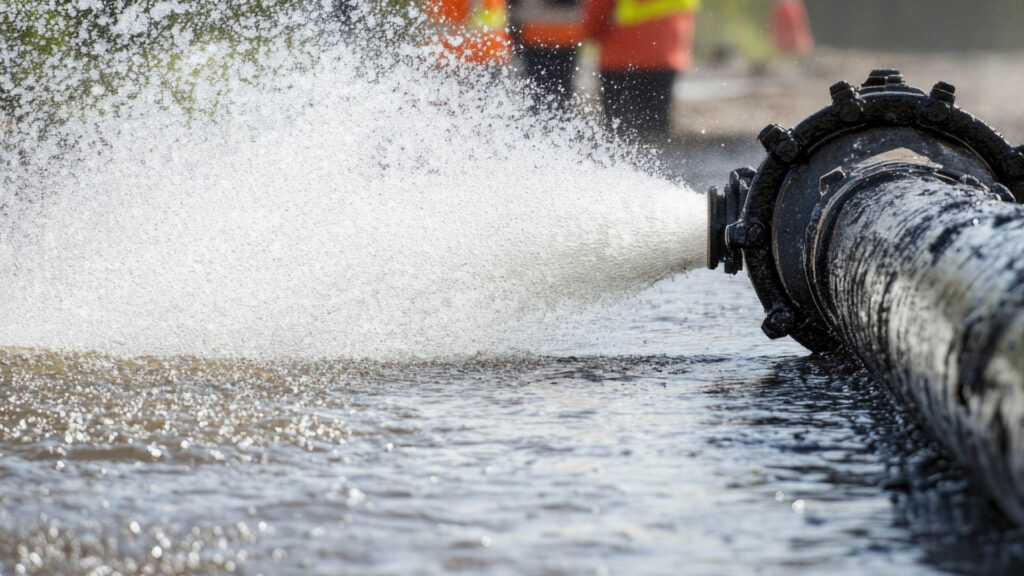
Mechanical seal failures can have far-reaching consequences across operational, financial, and environmental aspects of your business:
- Unscheduled Downtime
Failure of a mechanical seal often requires immediate shutdown of the equipment, leading to lost production and costly downtime. In high-throughput industries, even a few hours of lost productivity can equate to thousands or millions of dollars in lost revenue.
- Equipment Damage
When seals fail, lubricants or fluids can leak out, potentially causing damage to bearings, shafts, and other critical components, which may require a full rebuild or replacement.
Shaft sleeve scoring and bearing contamination are among the most common secondary damages resulting from mechanical seal failure.
- Environmental Hazards
Leaks of hazardous or toxic substances can pose significant environmental and safety risks, resulting in regulatory penalties and remediation costs. Mechanical seals are critical components in meeting environmental compliance standards and avoiding expensive fines.
Companies operating under EPA or OSHA regulations have little tolerance for uncontrolled leaks, making the reliability of mechanical seals a top priority.
- Increased Maintenance Costs
Frequent seal failures lead to higher maintenance expenses, including labor, spare parts, and emergency repairs, which can severely impact operational budgets over time.
Emergency shutdowns and overtime repair work are exponentially more costly than preventive maintenance and properly installed mechanical seals.
- Decreased System Efficiency
A leaking mechanical seal reduces system pressure and flow, making pumps and other rotating equipment less efficient and increasing energy consumption, which compounds operational costs.
Systematic losses due to poor sealing can also lead to increased wear on secondary components, such as impellers and casings.
How to Prevent Mechanical Seal Failures
Prevention is the key to extending the life of mechanical seals and maintaining operational reliability. Here’s how to proactively address the major causes of failure:
- Prioritize Proper Mechanical Seal Installation
Following best practices for mechanical seal installation is essential. Key points include:
- Verifying shaft condition and runout before installation.
- Using manufacturer-approved installation tools and lubricants.
- Recording installation data (torque values, alignment) for maintenance logs.
Training maintenance teams on mechanical seal technology and correct procedures can significantly reduce installation-related failures.
- Select the Right Mechanical Seal Technology
Choosing a seal type designed for your specific operating conditions is crucial. Factors to consider include:
- Temperature and pressure ratings
- Chemical compatibility
- Shaft speed and diameter
- Specific media being pumped
- External environmental factors (dust, humidity, corrosiveness)
Mechanical seal technology now includes options such as bellows seals, double cartridge seals, and gas seals, offering tailored solutions for various industries, including chemical processing and oil and gas.
- Implement Effective Lubrication and Flushing Plans
Proper lubrication and cooling of mechanical seals extend operating life and prevent common failure modes. Where applicable, installing seal flush systems, barriers, or external coolers helps support the performance of mechanical seal technology.
Choosing the correct flush plan (e.g., Plan 11, Plan 32) during mechanical seal installation is critical based on process requirements.
- Monitor and Minimize Vibration
High-precision mechanical seals demand tight tolerances for shaft alignment. Regular dynamic balancing, vibration monitoring, and bearing health assessments are key to minimizing seal face damage.
Maintenance teams should integrate vibration analytics into their predictive maintenance strategies.
- Control Temperature Variations
Seals must operate within their thermal limits. Operating outside these ranges can distort seal faces, elastomers, and even metallic components. Cooling jackets, heat exchangers, and insulating techniques should be employed when necessary to protect seals from extreme thermal shock.
- Perform Routine Inspections and Preventive Maintenance
Seal faces, elastomers, and hardware should be inspected during regular maintenance shutdowns. Look for wear patterns, surface scoring, cracking, and evidence of leakage. Proactive seal management programs can significantly increase uptime and equipment longevity.
The Role of Mechanical Seal Technology in Prevention
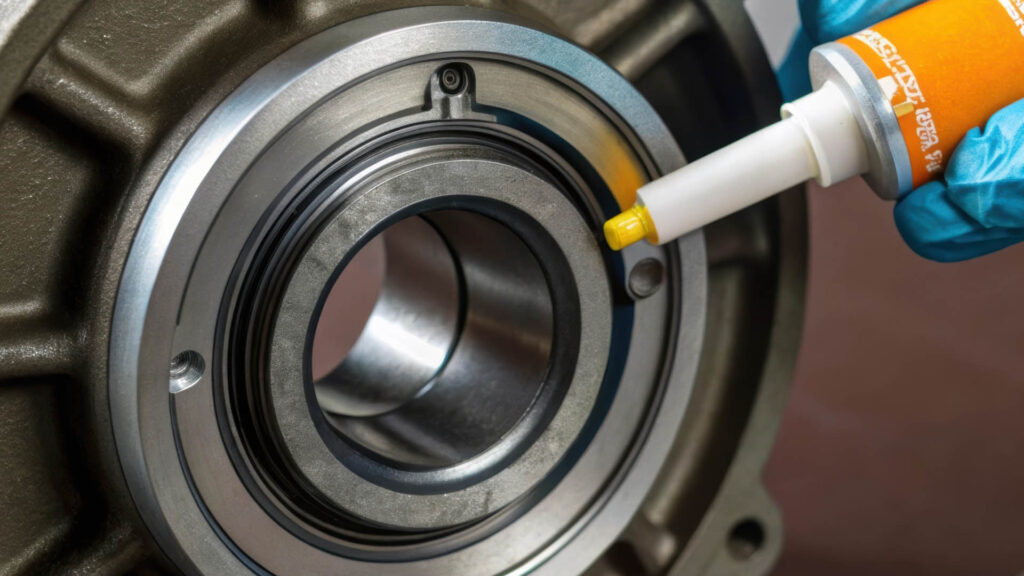
Today’s mechanical seal technology is designed with failure prevention in mind. Innovations include:
- Advanced face materials like silicon carbide and diamond-like coatings (DLC) to withstand abrasion and high temperatures.
- Pre-assembled cartridge designs that simplify mechanical seal installation and reduce user error.
- Pressurized dual seals that provide secondary containment and prevent hazardous leaks.
- Gas-lubricated seals offer non-contact operation for critical gas and vapor applications.
Choosing modern mechanical seal technology ensures you get greater tolerance to real-world operating conditions and reduced lifecycle costs.
Importance of Expert Mechanical Seal Installation
Even the most advanced mechanical seal technology will fail if the mechanical seal installation is not performed correctly. Partnering with experienced service providers like HydroMax Seal ensures:
- Detailed installation planning based on system conditions.
- Correct lubrication, torque, and positioning of mechanical seals.
- Verification of secondary systems, such as flush lines and cooling loops.
- Comprehensive testing before equipment commissioning to ensure seal integrity.
Proper mechanical seal installation directly translates to longer equipment life, better uptime, and lower total cost of ownership.
Additional Tips for Long-Term Seal Reliability
To further protect your investment in mechanical seals, consider implementing:
- Seal support systems (API plans) for critical pumps.
- Material upgrades when operating parameters exceed current seal capabilities.
- Operator training to recognize early symptoms of seal failure.
- Data logging for proactive seal performance tracking and failure analysis.
Partnering with a sealing solutions expert ensures that you always apply the latest mechanical seal technology advancements correctly.
Conclusion: Invest in Prevention, Not Repairs
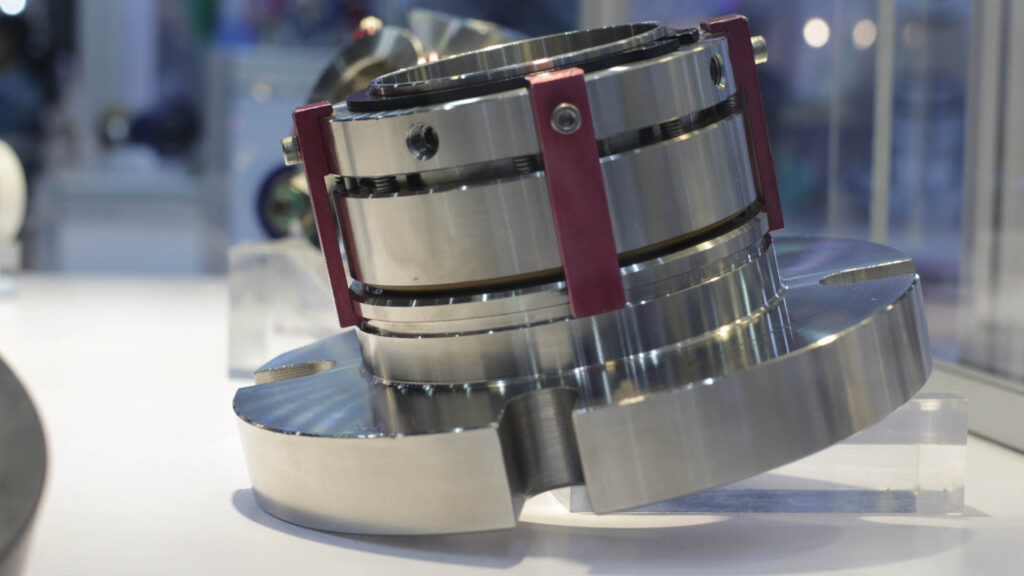
Mechanical seal failures are not inevitable. With the right combination of knowledge, proper mechanical seal installation, and the application of modern mechanical seal technology, you can significantly reduce failures, minimize downtime, and lower maintenance costs.
At HydroMax Seal, we combine engineering expertise, cutting-edge technology, and best-in-class services to help our clients maximize the reliability of their mechanical seals. Whether you need help selecting the right seal, expert installation support, or system audits, our team is ready to assist.
Looking to upgrade your sealing systems or solve persistent failure issues?
Contact HydroMax Seal today for tailored mechanical seal solutions that deliver reliability and performance.